Power Setting Help for an Arrow II
I feel very awkward about posting such a basic question given the expertise I have witnessed in many of these email threads. I also appreciate I have a lot to learn about my first aeroplane so please bear with me. However, this question is causing me sleepless nights!
I have recently purchased a 1974 PIPER PA-28R-200-2 with a LYCOMING IO-360-C1C with a MT-PROPELLER MTV-12-B/180-17.
When I took ownership of the Arrow I eagerly looked through the (very thin) POH looking for the recommended power settings for the cruse but I did not find any details. Not wanting to just rely on my instructor’s 24/24 or 25/25 in the cruse settings I downloaded a number of checklists which seemed to vary significantly.
I then downloaded the Lycoming Power settings for the engine (attached) which confused me (I am embarrassed to say)
Questions:
So at 75% @2000ft is it suggesting 24RPM and 25.2MAP? (Or the other way round?)
When running at 65% @2000ft why are there two settings? 21RPM and 25.4 MAP or 24RPM and 22.5?
I will of course go back to my instructor when he is back flying again. But wanted some advice so I could end my sleepless nights. Useful training links also appreciated.
Thanks, Ed
Ed Powell
Comments
Play around with different combinations...those numbers are just two different ways to get to your 75%, 65% etc... see what makes your engine run smoother. I grew up in the school where you always keep the RPMs equal to or above the MP, so that’s what I do, but there isn’t anything wrong with running the other set of numbers as long as it works with your engine and prop combo.
Jim M.
PA-28R-200
Based at BUU
ATC Chicago TRACON
Thanks for the comments and the suggestion... Really appreciate it. I was taught that as well Which is why I was confused by the chart.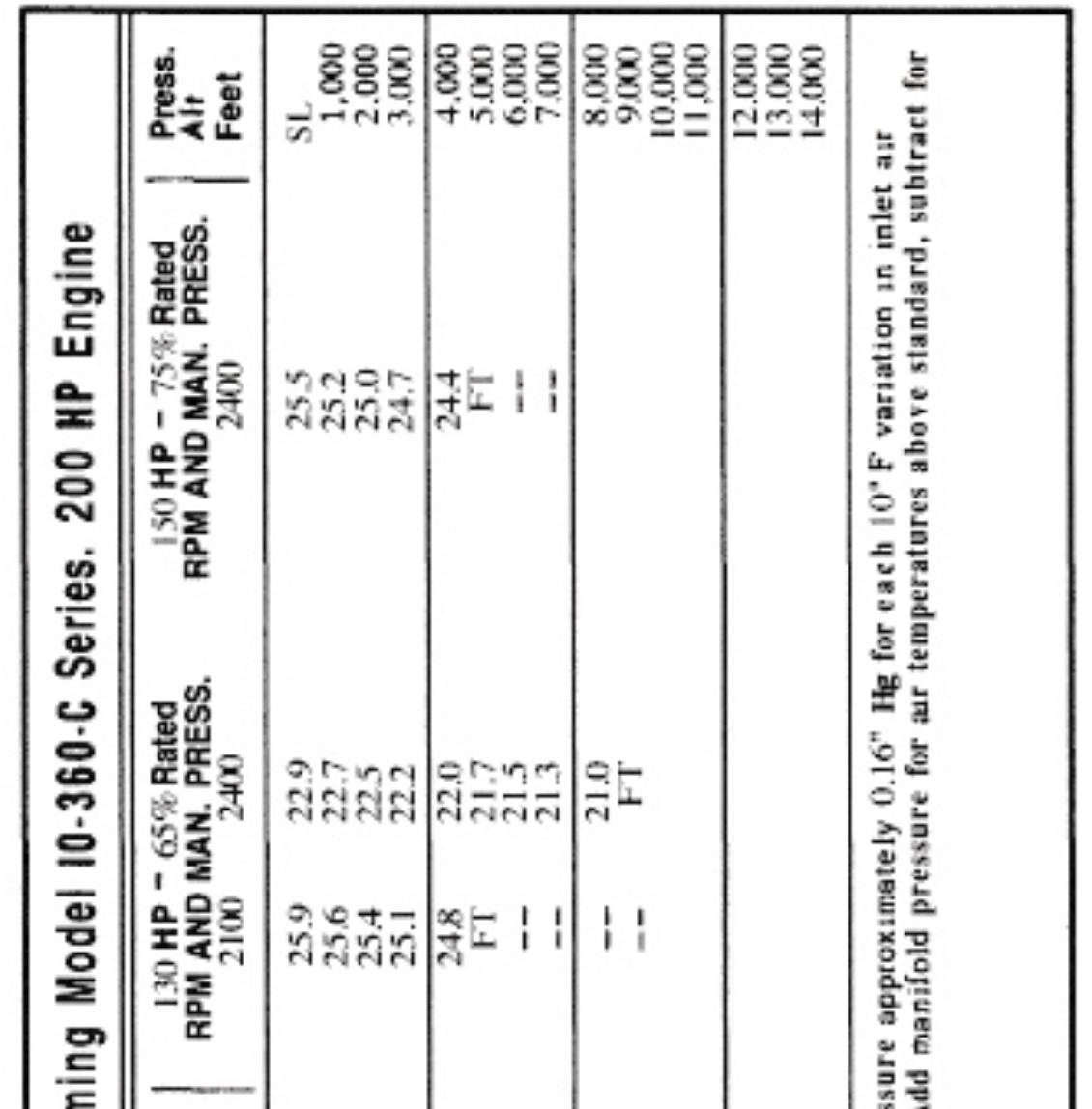
Ed Powell
Please don't feel awkward! We're all here to help and we're glad you're with us.
Scott Sherer
Wright Brothers Master Pilot, FAA Commercial Pilot
Ed...The same power can be achieved with high rpm and low MP or vice versa. Jimmy Doolittle's raiders made their one-way trip to Japan by running high MP and really low rpm because it conserved fuel. But the cylinder pressures can be high in that mode and that might cause excess oil consumption, at least that's what I've read. My Arrow has the same engine as yours although you must not have the 2000 to 2300 rpm limitation with the MT propeller. If you have an engine monitor that would be a big help so you can watch the cylinder head temps. Then experiment with the POH numbers. At my home base I never see more than 23 inches MP so that plus the rpm range limits my ability to experiment so please keep the forum appraised as to what you find!!
Jim Torley
CFI-A/I/G
1969 Arrow 200
Based at KFLY (Colorado Springs, CO)
Hey Jim,
Thank you so much for your reply. Very useful.
So I am taking from this that it does not really matter if you fly over squared or not (Oil and prop restriction depending..). Which makes sense given the table.
I am still trying to find out whether I have the prop restriction. It has recently had a new 3-blade prop (just before I bought it) so not sure if they changed the card on the gauge or not! I will strike up a conversation with the prop manufacture in Germany to check before using those cruse speeds.
As you can see from the video the range is restricted. (Shame I was not straight and level! As I usually get 5 or 10mph faster IAS)
Would be interested if you think I was running it too lean given the engine temps. And yes I think the analogue fuel flow is slightly out!
Always interested in any pointers!
Kind Regards, Ed
Ed Powell
If I knew how to add video's! I would be dangerous..
https://dropbox.com/s/8dopwovdfkyg1k0/IMG_9943.MOV?dl=0
Ed Powell
Your CHTs are perfect, all just over 300....I don’t think you have a problem there. I run well lean of peak at 65% power and my CHTs are usually right around 300 in cruise.
I put on a new prop last year (2-blade) and bought a new tach with the new red arc silk screened on it...if you find your new prop limitation doesn’t match the current tach, you can get a new one for only a couple hundred bucks.
I’m sure your prop manufacturer has the limitations for each engine/prop combo either on its website or can tell you over the phone or through email.
Jim M.
PA-28R-200
Based at BUU
ATC Chicago TRACON
Thanks for taking a look at it Jim! I am starting to understand it now.
Ed Powell
I was told by a Lycoming rep that the IO-360 cannot be hurt in any way by running higher MP, lower rpm. I typically economy cruise my Arrow IV at 2100-2200 rpm at 5500', with full throttle. At that altitude, full throttle equates to around 23" of manifold pressure. Running oversquare is much more of an issue with a turbocharged engine than with normally aspirated engines.
I love to defy gravity!
1979 Arrow IV
If it's on the power chart, it's okay. If it's not on the power chart, you're a test pilot.
Scott Sherer
Wright Brothers Master Pilot, FAA Commercial Pilot
Running oversquared is an issue with rotary engines, not so much with flat, horizontally opposed engines. That said, it's a bad habit and you really should not make it a regular thing. The one time in a thousand that you end up in a plane that has an engine that can't take it, and the next thing you know, there are cracks in the block and you're landing where you really don't want to. I will post a pic of an engine that recently had this happen. The guy had been told by the factory many times not to run oversquare, and he did anyway. I have never seen solid steel torn apart like that.
Running slower RPMs keeps the tach turning slower! To some, (tach time renters) that’s money in the bank!!!
Scott nailed it. The whole concept of "oversquare" and the idea that "oversquare=bad" has no basis in reality when it comes for typical GA engines. For example, my Continental TSIO-360 FB literally cannot be run "undersquare". Takeoff power is 41'/2575 RPM, and that is max continuous power BTW. 75% cruise is 33.8" at 2400 RPM, and the lazy 55% cruise is 29" at 2200 RPM.
Another example: the Diamond DA-40 with the Lycoming IO-360 M1A, normally aspirated. The manufacturer offers two options for 75% at MSL: 25.8' at 2400 RPM and 27.3" at 2200. Guess which one is the "recommended" one? Yep, the second one, more "oversquare".
As long as the POH says the MP/RPM combination is approved, choosing equivalent power setting with lower RPM is better for the engine wear, for your comfort, and for your pocket. As a PIC we have a choice, of course, but if I can, I will choose the combination with lower RPM. The only time when I decided to not pull the prop back was when I was flying a tired flight school airplane, with out-of-balance prop that would shake pretty badly if lower RPM was set.
Karol Zadora
PA28RT-201T Turbo Arrow IV
Seattle Area
Thank you to all those who have commented. I have found this thread very useful. Cheers, Ed
Ed Powell
First flight today with EDM-830. Tach and MAP are in agreement with EDM sensors. OAT needs a couple of degrees change compared to G5 sensor (which agrees with the Piper thermometer). Nice to have fuel required to destination instead of just to waypoints as in the FS-450. https://piperowner.org/talk/uploads/editor/kr/g51sgnpv4fja.jpg
Jim Torley
CFI-A/I/G
1969 Arrow 200
Based at KFLY (Colorado Springs, CO)
What kind of GPS are you using with the 830? My 830 is connected to my Avidyne 540 and I have a fuel range ring displayed on the gps. It shows 2 rings: A max-range and a reserve ring. Really a nice feature with your 830.
Scott Sherer
Wright Brothers Master Pilot, FAA Commercial Pilot
Scott, my GNS 530W drives the 830. I just tweaked some of the linear displays today. Haven't explored all the variables yet! I adjusted the OAT by 2 degrees to match the G-5. Did you do the HP ADJUST feature? It's going to be hard to get 70 % at this elevation . Doesn't really matter since the throttle goes to the wall on takeoff and doesn't move until I get ready to descend. It is what it is!!
Jim Torley
CFI-A/I/G
1969 Arrow 200
Based at KFLY (Colorado Springs, CO)
Good point, Jim. This is my first engine monitor in 8 airplanes and I'm hooked on it. The 830 is a very good value and highly functional. I don't know what I did without it, lol.
Scott Sherer
Wright Brothers Master Pilot, FAA Commercial Pilot
I have 1976 Arrow II with the same engine according to my POH, we have the Limitations: (continued): Placard:
On the instrument panel, between tachometer and manifold pressure guages station:
"Avoid continuous operation below 15 inches HG between 1900 RPM and 2350 RPM." According to mfg and my A&P its all about the counter balance with only IO 360 C1C.
Thanks, good to know
Scott Sherer
Wright Brothers Master Pilot, FAA Commercial Pilot
PA28R-200, 3 blade Hartzell
I climb WOT, 2500, 120 KIAS
5,500 cruise: WOT = 24”, Pull RPM to 2100, much smoother, quieter and lower fuel flow. LOP yields 8.3 GPH at 131 KTAS. At 9,000’, 21”, 2100 RPM 134 KTAS. If fighting a headwind, 2400 RPM and min 75 ROP adds 15 kts. I avoid any ROP less than 75, see Lycoming chart. Peak CHTs occur about 30 ROP.
1969 PA28R-200
Some day the turbulence will go away and I can experiment with LOP but I am used to running at peak EGT which, at my normal cruise altitude of about 10 k results in about 8.8 gph and TAS of 143-145 kts (see previous photo posted) WOT, of course, for a non-turbo!!! I know LOP has some detractors and proponents but I'm primarily interested in preserving the NEW engine so without Gami injectors I'll stay ROP.
Jim Torley
CFI-A/I/G
1969 Arrow 200
Based at KFLY (Colorado Springs, CO)
At 10K I don’t think you can generate the power required to hurt your engine either way. With that said, being the other Arrow guy with a new engine, but also a low-lander, I fly LOP, but also keep my cruise power at 65% or less. I’m not as concerned with finding the “optimum” mixture setting as much as I am with a smooth running engine and low CHTs.
In cruise I get CHTs of 300F +/- 10 and about 9.7 GPH with a power setting of 22”/2400RPM.
I get a headache at 10K
Jim M.
PA-28R-200
Based at BUU
ATC Chicago TRACON
Also, 76R, our panels look almost identical with the JPI and the G5’s all in the same place! If you ever accidentally end up in my Arrow, you’d feel right at home.
Jim M.
PA-28R-200
Based at BUU
ATC Chicago TRACON
Jim M.
PA-28R-200
Based at BUU
ATC Chicago TRACON
I experimented the other day with the EDM-830 and at a density altitude of 10,500 (8500 true, 18 C, 30.32 Hg) and 2380 rpm (WOT), 22.8 in MAP, fuel flow was 8.8 gph (about 50 ROP) for TAS of 143 kts. See the photo I posted the other day.
Jim Torley
CFI-A/I/G
1969 Arrow 200
Based at KFLY (Colorado Springs, CO)
Jim M...Yes, at first glance they are really similar! Your compass mounting and the secondary AI gave it away for me!!
Jim Torley
CFI-A/I/G
1969 Arrow 200
Based at KFLY (Colorado Springs, CO)
If you’re getting 8.8gph ROP, I’m curious to see your LOP numbers!
Jim M.
PA-28R-200
Based at BUU
ATC Chicago TRACON
Since those numbers were almost at peak EGT (the way I usually fly) perhaps the LOP won't be significantly different. I would like to have a vernier control for the mixture since it is really hard to adjust the mixture in small increments to find peak when it is moderate turbulence. I usually lean the mixture until all cylinders max EGT then add a tenth or 2 gph just to stay ROP but didn't attempt to achieve a specific temp difference. I noticed in your photo that the cylinder temps were quite low compared to mine and the EGT was lower also. But you were running 9.6 gph at 1000 feet higher. So you must have been running ROP by a decent temp difference. More experimentation for sure!
Jim Torley
CFI-A/I/G
1969 Arrow 200
Based at KFLY (Colorado Springs, CO)